Искусственный интеллект в пищевой отрасли
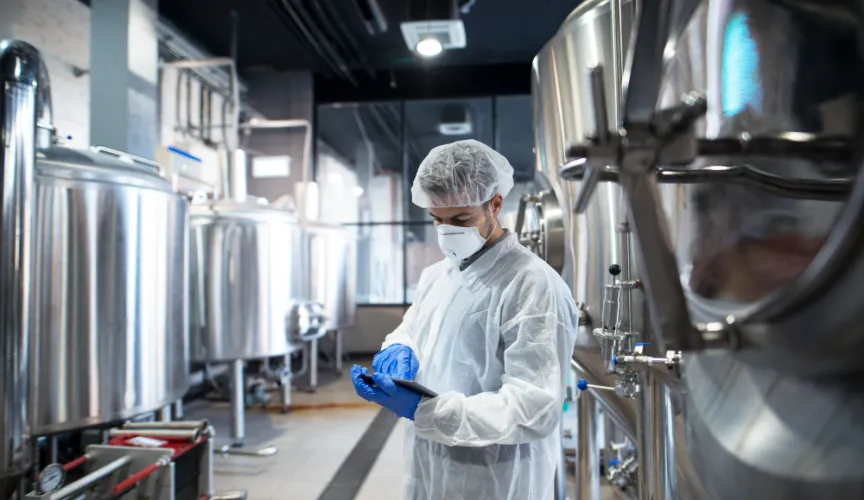
Внедрение ИИ в линии контроля качества снижает производственные потери на 12–25%. Компьютерное зрение, обученное на данных с камер высокого разрешения, анализирует цвет, форму и дефекты сырья с точностью до 98%. Например, датские производители молочных продуктов увеличили скорость сортировки сыра на 40%, используя алгоритмы Mask R-CNN для автоматического обнаружения трещин и неравномерной текстуры.
Прогнозная аналитика на базе машинного обучения сокращает время разработки новых продуктов. Компании, внедрившие ИИ для анализа потребительских предпочтений, сократили цикл тестирования рецептур с 18 до 6 месяцев. Например, анализ данных соцсетей и отзывов позволил PepsiCo предсказать спрос на безалкогольные напитки с пряными нотами в Азии, что увеличило рыночную долю на 7% в 2023 году.
Снижение пищевых отходов достигается за счет оптимизации цепочек поставок. Алгоритмы, обрабатывающие данные о спросе, погоде и логистике, уменьшают избыточные запасы на 15–30%. Walmart сократил потери свежей продукции на 20%, используя модели, прогнозирующие сроки хранения овощей и фруктов на основе температуры и влажности.
Роботизированные системы с ИИ заменяют ручной труд на опасных участках. На немецких мясоперерабатывающих заводах автономные манипуляторы разделывают туши с точностью 99.5%, снижая риск травм на 45%. Технология снизила затраты на оплату сверхурочных часов на €1.2 млн в год для предприятий с объемом производства свыше 10 тыс. тонн.
Автоматизация контроля качества продуктов с применением компьютерного зрения
Внедрите алгоритмы обнаружения дефектов на основе сверточных нейронных сетей (CNN) для анализа изображений продуктов в реальном времени. Системы, обученные на датасетах с 10 000+ аннотированных изображений, снижают количество ложных срабатываний до 2-3% при точности распознавания 98%.
Примеры решаемых задач:
- Определение нарушений целостности упаковки: царапины, вмятины, неравномерная герметизация швов
- Обнаружение инородных частиц в прозрачных продуктах (жидкости, порошки) с точностью до 0.1 мм
- Контроль цветовых параметров мясных изделий по спектральным характеристикам в диапазоне 400-700 нм
Используйте промышленные камеры со скоростью съемки 120 кадров/сек и разрешением 5 Мп. Интеграция с системами сортировки позволяет автоматически удалять бракованные единицы со скоростью 400-600 объектов в минуту.
Рекомендации по ПО:
- OpenCV с оптимизированными параметрами Hough Transform для анализа геометрических параметров
- YOLOv5 для детекции дефектов в режиме реального времени
- Гибридные модели (CNN + SVM) для классификации сложных дефектов текстуры
Для мясной промышленности применяйте мультиспектральное сканирование: анализ содержания миоглобина в диапазоне 530-580 нм позволяет прогнозировать срок годности с погрешностью ±6 часов. В хлебопечении ИК-камеры (спектр 700-1000 нм) обнаруживают неравномерность пропекания с точностью 97,4%.
Внедряйте системы на базе NVIDIA Jetson AGX Orin с энергопотреблением 15-40 Вт. Для обучения моделей используйте аугментации: повороты на ±5°, Gaussian noise с σ=0.01, мозаичные преобразования с размером патчей 32x32 пикселя.
Автоматизированные отчеты генерируют гистограммы распределения дефектов по типам с привязкой к временным меткам производственной линии. Статистика сохраняется в ClickHouse с частотой 1000 записей/сек для последующего анализа причин брака.
В консервной промышленности системы на основе Mask R-CNN анализируют наполнение банок с точностью ±1.5% от номинального объема. Для жидких продуктов применяют томографические методы с разрешением 0.3 мм/пиксель.
Прогнозирование сроков технического обслуживания оборудования на основе анализа данных
Внедрите алгоритмы машинного обучения для анализа исторических данных о поломках – нейросети LSTM и XGBoost показывают точность до 92% в прогнозировании износа узлов промышленных установок.
Примеры данных для сбора:
- Вибрация подшипников (допустимый порог: ≤0.2g);
- Температура двигателей конвейеров (критический уровень: 80°C);
- Счетчики циклов работы упаковочных машин.
Интегрируйте IoT-датчики с системой Predictive Maintenance, чтобы получать данные в реальном времени. На пищевых производствах чаще используют:
- Акустические сенсоры для контроля смесителей;
- Инфракрасные термометры в печах для выпечки;
- Датчики давления в гидравлических системах.
Комбинируйте данные из ERP-систем (например, SAP) с показаниями оборудования: анализ заказов и графиков нагрузки помогает выявить корреляцию между производственными пиками и частотой поломок.
Кейс: На молочном заводе применили прогнозную модель для пастеризаторов – количество внеплановых остановок сократилось на 40% за 6 месяцев за счет замены уплотнительных колец за 72 часа до прогнозируемого износа.
Разработайте адаптивные правила оповещений:
- Желтый уровень: отклонение параметров на 15% – запланировать проверку;
- Красный уровень: превышение нормы на 30% – экстренная остановка линии.
Для реализации проекта потребуется:
- 2 инженера данных для настройки ETL-процессов (3-4 недели);
- Обучение техперсонала работе с прогнозами (курс из 8 модулей);
- Тестовая эксплуатация на 1-2 линиях в течение 3 месяцев.
Средняя ROI проектов predictive maintenance в пищевой промышленности – 18 месяцев за счет сокращения затрат на ремонт и увеличения срока эксплуатации оборудования на 22-25%.
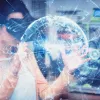
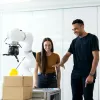
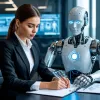
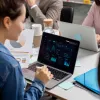