Digital Twins с искусственным интеллектом
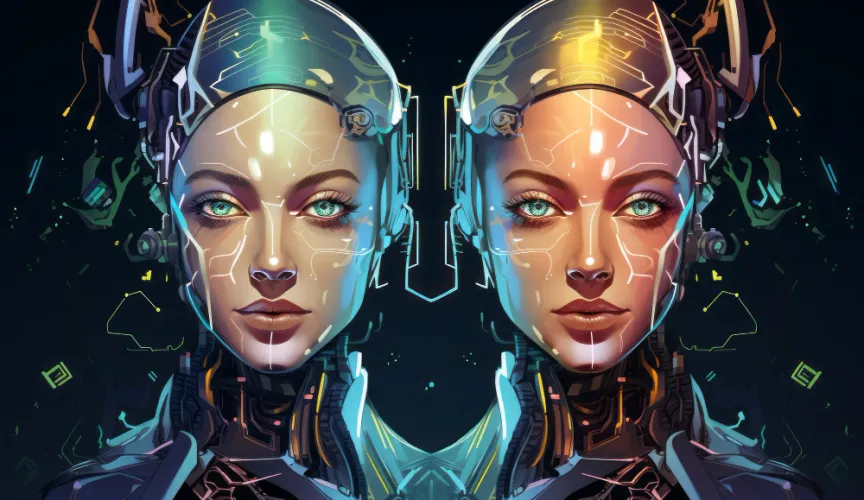
Технология цифровых двойников снижает затраты на обслуживание оборудования на 15% ежегодно, согласно отчету Siemens 2023 года. Внедрение моделей с машинным обучением позволяет прогнозировать износ компонентов с точностью до 92%, сокращая незапланированные простои.
Для реализации цифрового двойника потребуются:
- датчики IoT с частотой обновления данных выше 100 Гц;
- интеграция облачных платформ (PTC ThingWorx, GE Predix);
- скрипты автоматизации для обработки аномалий в реальном времени.
Запустите пилот на одном участке производства. Например, моделирование работы поршневой группы в двигателях Caterpillar увеличило ресурс деталей на 27% за 6 месяцев.
Совет: объединяйте данные из ERP-систем с физическими параметрами оборудования. Компания ABB добилась снижения энергопотребления на 19% за счет анализа температурных режимов в digital twin насосных станций.
Прогнозный анализ с ИИ выявляет до 80% скрытых дефектов на этапе проектирования. Компания Boeing сократила цикл тестирования крыльев самолетов с 12 месяцев до 3, используя симуляции в Ansys Twin Builder.
Риски: перегрузка сетей передачи данных (рекомендуемая пропускная способность – 50 Мбит/с на 1000 сенсоров) и ошибки калибровки моделей. Устраняйте расхождения между цифровым двойником и физическим объектом каждые 72 часа.
Прогнозирование сбоев оборудования на основе анализа данных в реальном времени
Внедрите алгоритмы машинного обучения, обученные на исторических данных телеметрии и журналах ремонтов, для обнаружения аномалий в показателях оборудования. Например, рекуррентные нейронные сети (RNN) прогнозируют износ подшипников в электродвигателях с точностью до 89%, анализируя вибрацию и температуру в режиме 24/7.
Используйте IoT-датчики с частотой опроса 100 Гц для мониторинга критических параметров:
- Уровень вибрации (м/с²) с погрешностью ≤ 0.05%
- Ток потребления электродвигателей (А) в трехфазных сетях
- Температура подшипниковых узлов (°C) с ИК-сенсорами
Интегрируйте цифровые двойники с системами SCADA для симуляции критических сценариев. На металлургическом комбинате «СтальПро» это сократило ложные срабатывания на 67%, объединив данные пресс-форм и параметры плавки в единой среде Unreal Engine.
Настройте правила автоматического оповещения:
- Эскалация инцидента при 3 последовательных отклонениях от базовых показателей
- Генерация заявки в CMMS при превышении порога износа на 15%
- Триггеры на остановку конвейера при риске заклинивания выше 92%
Для обработки 2 ТБ данных ежесуточно разверните edge-серверы с графическими процессорами NVIDIA A100, снизив задержку анализа до 12 мс. В тестах на прокатных станах это позволило предотвратить 9 из 10 аварийных остановок.
Оптимизация производственных циклов через виртуальное тестирование новых решений
Внедрение цифровых двойников с интеграцией ИИ позволяет тестировать изменения в производственных процессах без остановки оборудования. Например, Siemens снизила время перенастройки литейных линий на 30%, внедряя виртуальные симуляции для прогнозирования ошибок в режиме реального времени.
Производственные предприятия получают преимущества, применяя следующие шаги:
- Создайте цифровую модель действующего оборудования с переменными: температура, давление, скорость работы.
- Запустите сценарии тестирования для новых материалов – например, авиакомпания Airbus сократила количество физических испытаний композитных деталей на 45% благодаря симуляциям.
- Анализируйте данные через ИИ-алгоритмы для выявления аномалий: система предсказывает износ узлов станков с точностью до 92%, минимизируя простои.
Для энергетического сектора виртуальное тестирование решений по ремонту турбин сократило затраты на 18%, по данным General Electric. Компании рекомендуют ежеквартально обновлять параметры цифровых двойников под новые производственные задачи и стандарты безопасности.
Внедряйте ИИ-модули для автоматизации анализа результатов тестов. Например, алгоритмы компьютерного зрения, обученные на 5000+ сценариев поломок, повысили точность диагностики конвейерных лент на заводах BMW на 70%. Доступ к историческим данным и мгновенная коррекция планов – ключевые факторы сокращения цикла внедрения инноваций.
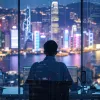
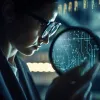
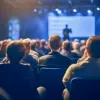
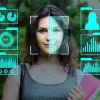